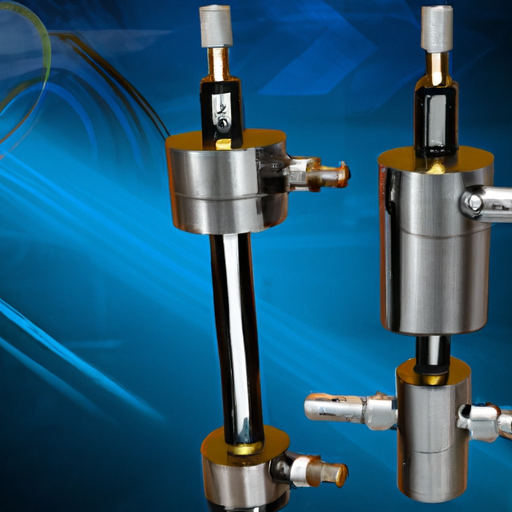
Have you ever wondered what sets hydraulic systems apart? In this article, we will explore the key differences between hydraulic systems and other types of systems. From their working principles to their applications, we will shed light on the unique characteristics that make hydraulic systems a popular choice in various industries. So, if you’re curious to learn more about the nuances of hydraulic systems, read on for an enlightening journey into their fascinating world.
Basics of Hydraulics
Definition of hydraulics
Hydraulics is a branch of engineering that deals with the mechanical properties of liquids and the application of fluid power. It involves the use of pressurized liquids to generate, control, and transmit power. In simple terms, hydraulics is the utilization of fluid mechanics to perform various tasks.
Principle and operation of hydraulics
The principle behind hydraulics is based on Pascal’s law, which states that when pressure is applied to a fluid in a confined space, it is transmitted equally in all directions. This principle forms the basis of hydraulic systems, where a small force can be magnified by using a fluid-filled system to achieve a greater output force. Hydraulic systems operate by pumping fluid into an enclosed space, which then exerts pressure on a piston or other mechanical components.
Components of a hydraulic system
A hydraulic system consists of several key components that work together to perform specific functions. These components include a hydraulic pump, which generates the flow of fluid; hydraulic cylinders or motors, which convert fluid energy into mechanical force; hydraulic valves, which control the flow and direction of the fluid; and hydraulic fluids, which transmit power and lubricate the system. Additionally, filters, accumulators, hoses, and fittings are also common components of hydraulic systems.
Types of Hydraulic Systems
Open-loop hydraulics
Open-loop hydraulic systems, also known as simple hydraulic systems, are characterized by a one-way flow of hydraulic fluid. In these systems, the fluid is used once and then discharged. Open-loop systems are commonly used in applications where precise control is not required, such as in simple machinery or agricultural equipment.
Closed-loop hydraulics
Closed-loop hydraulic systems, also called hydrostatic systems, are designed to recycle the hydraulic fluid. These systems circulate the fluid through a closed circuit, allowing for continuous operation and improved efficiency. Closed-loop systems are commonly used in applications where precise control and high efficiency are essential, such as industrial machinery and heavy equipment.
Semi-closed loop hydraulics
Semi-closed loop hydraulic systems combine the features of both open-loop and closed-loop systems. They allow for partial recycling of the hydraulic fluid while still maintaining simplicity and cost-effectiveness. Semi-closed loop systems are often used in applications where intermittent operation is required, such as in construction machinery.
Comparing Different Hydraulic Systems
Benefits of open loop systems
Open-loop systems offer simplicity and cost-effectiveness due to their uncomplicated design. They are easy to install and maintain, making them ideal for applications where precise control is not necessary. Additionally, open-loop systems operate at lower pressures, resulting in reduced energy consumption and lower operational costs.
Drawbacks of open loop systems
One of the major drawbacks of open-loop systems is their inefficiency, as they continuously discharge hydraulic fluid. This constant fluid loss can lead to increased environmental impact and the need for frequent fluid replacement. Additionally, open-loop systems are less precise in their control, making them unsuitable for applications that require high accuracy.
Benefits of closed loop systems
Closed-loop systems offer improved efficiency and precise control over hydraulic functions. By recycling the hydraulic fluid, these systems minimize fluid loss and reduce the need for frequent fluid replacement. Closed-loop systems also provide better control over speed, force, and direction, making them suitable for applications that require high accuracy and responsiveness.
Drawbacks of closed loop systems
The complexity of closed-loop systems often translates into higher installation and maintenance costs. The use of filtration systems and heat exchangers to maintain fluid quality and temperature further adds to the costs. Additionally, closed-loop systems require a higher initial investment due to their advanced components and technology.
Benefits of semi-closed loop systems
Semi-closed loop systems offer a balance between the simplicity of open-loop systems and the efficiency of closed-loop systems. They provide the advantage of partial fluid recycling, resulting in reduced fluid consumption and environmental impact. Semi-closed loop systems also offer better control compared to open-loop systems, making them suitable for applications that require intermittent operation.
Drawbacks of semi-closed loop systems
While semi-closed loop systems provide an intermediate solution, they may not offer the same level of efficiency and precision as closed-loop systems. The partial fluid recycling may still require regular fluid replacement, which can increase maintenance costs over time. Additionally, semi-closed loop systems may not be suitable for high-demand applications that require continuous operation.
Hydraulic Fluids
Types of hydraulic fluids
Hydraulic fluids can be broadly categorized into two types: mineral-based and synthetic-based. Mineral-based fluids, often referred to as hydraulic oil, are derived from petroleum and offer good lubrication properties. Synthetic-based fluids, on the other hand, are made from synthetic materials and offer improved performance in terms of temperature resistance, viscosity index, and environmental impact.
Purpose of hydraulic fluids
Hydraulic fluids serve several important purposes in hydraulic systems. They act as a power transmission medium, transferring force from the hydraulic pump to the hydraulic cylinders or motors. Hydraulic fluids also provide lubrication, reducing friction and wear between moving components. Additionally, they help dissipate heat generated during system operation, preventing overheating and damage.
When to change hydraulic fluids
Regular fluid maintenance is essential to ensure the proper functioning of hydraulic systems. The frequency of fluid changes depends on various factors, including operating conditions, system design, and fluid type. Generally, hydraulic fluids should be changed if they become contaminated, degraded, or if there are significant changes in system performance. Regular fluid analysis and periodic inspections can help determine the appropriate timing for fluid changes.
Hydraulic Pumps
Types of hydraulic pumps
Hydraulic pumps are responsible for generating the flow of hydraulic fluid in a hydraulic system. There are several types of hydraulic pumps, including gear pumps, vane pumps, piston pumps, and axial piston pumps. Each type has its own advantages and limitations, making them suitable for different system requirements.
Working of the pumps
Hydraulic pumps work by converting mechanical energy, provided by an engine or motor, into hydraulic energy. This conversion is achieved through the movement of pump components, such as gears, vanes, or pistons. As the pump components rotate or reciprocate, they create a pressure difference in the fluid, causing it to flow and generate hydraulic power.
Difference in hydraulic pumps based on system type
The selection of hydraulic pumps depends on the type of hydraulic system being used. Open-loop systems often utilize gear pumps or vane pumps due to their simplicity and cost-effectiveness. Closed-loop systems, on the other hand, often require more advanced pumps, such as piston pumps or axial piston pumps, to provide the precise control and higher efficiency necessary for their operation.
Hydraulic Valves
Role of valves in hydraulic systems
Valves play a critical role in hydraulic systems by controlling the flow, pressure, and direction of the hydraulic fluid. They act as flow regulators, allowing operators to adjust the speed and force of hydraulic components. Valves also ensure the proper sequencing of hydraulic functions and provide safety features, such as pressure relief and overload protection.
Types of valves
There are various types of hydraulic valves, each serving a specific purpose within a hydraulic system. Common types of valves include directional control valves, pressure control valves, flow control valves, and check valves. Each valve type has its own design and operating principles, enabling specific control functions within the system.
How different system types affect valve selection
The selection of hydraulic valves depends on the specific requirements of the hydraulic system. Open-loop systems typically utilize simpler directional control valves and basic pressure control valves. Closed-loop systems often require more precise and responsive valves, such as proportional control valves or servo valves, to achieve the desired level of control. The selection of valves is influenced by factors such as system pressure, flow rate, accuracy, and response time.
Hydraulic Cylinders and Motors
Function of hydraulic cylinders and motors
Hydraulic cylinders and motors are key components of hydraulic systems that convert hydraulic energy into mechanical force or rotational motion. Hydraulic cylinders are used to generate linear motion, often in the form of pushing or pulling, while hydraulic motors generate rotary motion. These components provide the driving force necessary for various applications, such as lifting, pushing, pulling, or rotating.
Common types
There are several types of hydraulic cylinders commonly used in hydraulic systems, including single-acting cylinders, double-acting cylinders, and telescopic cylinders. Single-acting cylinders exert force in one direction and use external forces, such as gravity or springs, to return to their original position. Double-acting cylinders, on the other hand, exert force in both directions using hydraulic pressure. Telescopic cylinders consist of multiple nested stages, allowing for extended reach without sacrificing compactness.
Variation based on system types
The selection of hydraulic cylinders and motors depends on the specific requirements of the hydraulic system. Open-loop systems often utilize simpler and less expensive cylinders and motors due to their less demanding control requirements. Closed-loop systems, on the other hand, often require more advanced and precise cylinders and motors to meet the high accuracy and responsiveness needed for their operation.
Safety Measures for Hydraulics
Hazards associated with hydraulics
Working with hydraulics can present various hazards if not handled properly. Some common hazards include high pressure, fluid injection injuries, hydraulic fluid hazards, electrical hazards, and machine entanglement. These hazards can lead to serious injuries or even fatalities if appropriate safety measures are not taken.
Safety gear for hydraulic system handling
To ensure safe handling of hydraulic systems, it is important to use appropriate safety gear. This includes wearing protective gloves, goggles, and clothing to protect against hydraulic fluid exposure and potential injuries. Safety factors such as pressure relief valves, flow controls, and emergency stop systems should also be incorporated into the design of hydraulic systems.
Routine checks and maintenance
Regular checks and maintenance are crucial to ensure the safe operation of hydraulic systems. This includes inspecting hydraulic hoses, fittings, and connections for any signs of wear or leaks. Regular fluid analysis and changes, as well as filter replacements, should also be performed according to manufacturer recommendations. Additionally, operators should receive proper training on the safe operation and maintenance of hydraulic systems.
Applications of Hydraulics
Use of hydraulics in different industries
Hydraulics find wide applications in various industries due to their ability to provide powerful and precise control. In the construction industry, hydraulic systems are used in excavators, cranes, and heavy machinery for lifting and pushing tasks. In the automotive industry, hydraulics are used in braking and steering systems to enhance safety and control. Other industries, such as aerospace, agriculture, marine, and manufacturing, also rely on hydraulics for their specific applications.
Importance of hydraulics in modern machinery
Hydraulics play a crucial role in modern machinery, enabling precise control, increased power output, and enhanced productivity. The use of hydraulics allows for the design of compact and efficient systems that can perform heavy-duty tasks. The ability to control speed, force, and direction with precision makes hydraulic systems indispensable in many industries. Furthermore, advancements in hydraulic technology continue to drive innovation and improve the performance of modern machinery.
Future of Hydraulics
Current technological advancements
Hydraulic technology continues to evolve, with ongoing advancements aimed at improving efficiency, performance, and sustainability. The use of electronic control systems and sensors allows for more precise control and real-time monitoring of hydraulic systems. The integration of smart technology and automation is also becoming more prevalent, enhancing efficiency and reducing human error in hydraulic operations.
Predicted changes in hydraulic technologies
The future of hydraulics is likely to see further improvements in energy efficiency, reduced environmental impact, and enhanced reliability. The development of more advanced hydraulic fluids and components will contribute to achieving these objectives. There is also a growing focus on electrification and hybridization of hydraulic systems, combining the benefits of both hydraulic and electric technologies. These advancements will lead to more sustainable and environmentally friendly hydraulic systems.
Sustainability in hydraulics
As sustainability becomes increasingly important, the hydraulic industry is actively seeking ways to minimize its environmental impact. This includes the development of bio-based and eco-friendly hydraulic fluids, as well as the use of regenerative technologies to recover and recycle energy. The integration of renewable energy sources, such as solar or wind, into hydraulic systems is also being explored to further reduce the reliance on fossil fuels.
In conclusion, hydraulics is a fundamental engineering discipline that offers significant advantages in terms of power, control, and efficiency. Understanding the basics of hydraulics, different system types, components, and safety measures is crucial for the successful design, operation, and maintenance of hydraulic systems. With ongoing advancements and a focus on sustainability, the future of hydraulics looks promising, promising continued improvements in performance and reduced environmental impact.